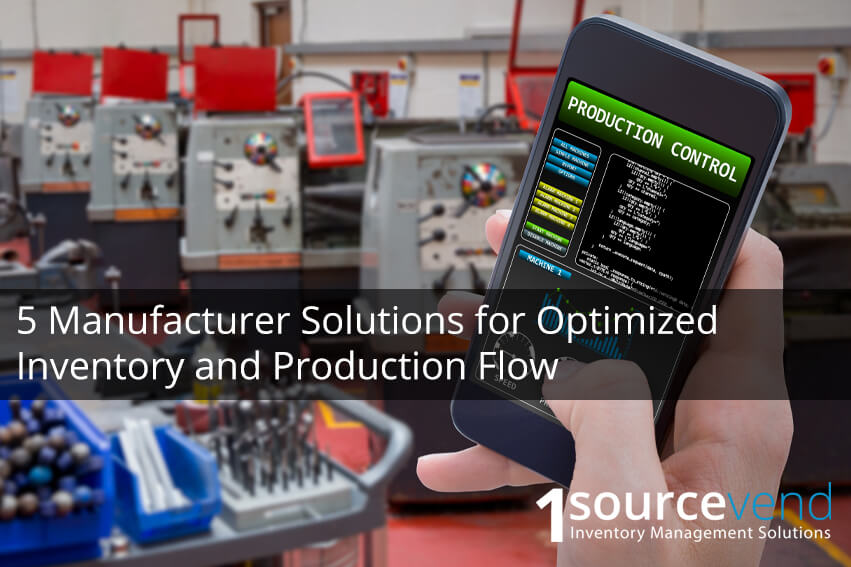
Looking to improve productivity and inventory management at your manufacturing facility?
Every business, no matter the industry, wants to operate more profitably. Most times, this is achieved by reaching the maximum output possible without sacrificing time, quality, safety or margin.
However, many businesses fail to reach production benchmarks due to hidden inefficiencies that threaten an organization’s resources.
Missing tools, inventory shortages, machine malfunctions, performance loss — there are a thousand reasons why your production line isn’t seeing the return it should.
The truth is that you can’t solve problems you don’t know exist. That’s why it’s critical that management continuously looks for areas to improve, redefine and reorganize existing processes.
That’s easier said than done, especially in businesses unaccustomed to change.
“It’s how we’ve always done it.”
To break that cycle, organizations must periodically take a step back and evaluate current processes, challenge the status quo and adopt new strategies.
Are you looking for ways to increase efficiency in your operations? Want to:
- Reduce waste
- Reduce downtime
- Improve throughput
- Improve product quality
- Minimize worker injury
- Increase profits
- Improve supply chain visibility
Then, maybe it’s time to reevaluate your plant’s production flow.
Curious if vending can help your business? Download A Distributor’s Guide to Best Practices in Vending & Inventory Control.
Why Should Production Flow Optimization be a Priority in Manufacturing?
Production flow is how well all the parts of an operation move along each stage of the process from raw materials to the finished products.
Manufacturing processes that operate optimally produce consistent and reliable results, critical components that lay the groundwork for long-term success. Not only will an efficient production flow help you monitor spend and lower the cost to produce finished goods, but it will also help improve quality and customer satisfaction.
5 Ways to Improve Efficiency on the Production Floor
It’s illogical to consider a complete overhaul in your manufacturing processes. Instead, small, incremental and continuous improvements over time enable managers to spot breakdowns in operations, identify solutions and track the progress of each change.
Here are a few jumping-off points that can begin to address your organization’s challenges and get you on your way to better production efficiency:
Implement a 5S Methodology to Reduce Waste
Waste is a profit killer and can result from inefficient use of materials, energy, labor or space. Cluttered workstations, missing inventory, lost tools and grimy machinery are just a few subtle examples of how time, money and resources can be wasted slowly over time.
5S is a lean methodology that improves workplace efficiency by implementing a systematic framework for organization and cleanliness. There are five steps in the system, each starting with the letter S:
- Sort: Remove unnecessary items from each work area.
- Set in Order: Organize and identify storage solutions for efficient use.
- Shine: Clean and inspect work areas and machines regularly.
- Standardize: Schedule regular cleanings and maintenance activities using a clearly communicated standard operating procedure (SOP).
- Sustain: Make organization a way of life by assigning responsibility to tasks, tracking progress and continually improving.
Reconfigure Plant Layout for Better Production Flow
Your manufacturing facility’s layout and design are one of the most important aspects of a business’s overall operations. Like the floor plan of a house, the placement of materials, equipment and employees can either help or hinder the flow of information, goods or activity in your production line.
One significant benefit of a strategic plant layout is maximized production volume per square foot. Are there areas of your production floor that are stacked with inventory or spare parts instead of being used for production? Consider mapping out your current plant layout and strategically plan for placement of workstations and supply storage to maximize productivity.
In addition to increased efficiency, a proper layout can offer added visual control. Knowing what’s happening in every area of your plant enables you to spot potential bottlenecks and troubleshoot solutions before they become a bigger problem.
Introduce Point-of-Use Supply Solutions for Improved Efficiency
Are your workers walking back and forth in your facility to obtain the parts and supplies required to perform routine tasks? Those steps add up over time, not only creating production bottlenecks but also increasing the likelihood of worker fatigue.
Strategically placed industrial vending machines offer employees round-the-clock point-of-use dispensing on a wide variety of mission-critical items.
Industrial vending machines and lockers have gained popularity among manufacturing facilities for some time as an effective inventory control solution for consumables as well as high-dollar items. With vending, mission-critical supply items are readily available at the point of use, minimizing the time employees spend searching for tools and parts to do their job. Users only have to enter a PIN or swipe a card for access to products, improving employee accountability and productivity. Learn more.
Vend supplies like:
- Safety and personal protective equipment (gloves, safety glasses, earplugs, hard hats, respirators, first aid, monitors, etc.)
- Power, hand and cutting tools, plus batteries and accessories
- MRO (Maintenance, repair and operating) items
- Uniforms
- Hydration supplies
Rethink Technology Solutions for Better Production Flow
Thanks to advancements in technology and lower costs of entry, businesses of all sizes can begin making more informed operational decisions based on data. New tech options that can optimize your production line include:
- Automated Storage and Retrieval Systems (AS/RS systems) are computer-controlled systems that can move loads in and out of storage through a series of conveyors or automated guided vehicles. AS/RS systems are ideal for moving consistent loads needed for manufacturing processes and can reduce the labor required in transport as well as save space and track inventory.
- Inventory Control Software is an essential tool that offers businesses added visibility into stocked items in real-time; helping you track trends and generate reports like employee usage, product pricing and inventory levels. Controlled employee access, usage reports and reduced stock-outs are just a few of the benefits inventory control software has to offer.
- Warehouse Technology can take your inventory management to the next level. Barcodes and scanners allow you to scan and track a wider selection of inventory items in any storeroom/warehouse scenario. The data is then synced with the company’s inventory control software for complete reporting and management throughout the facility. Learn more.
Dig into Data for Better Decision-Making Capabilities
There are five simple steps to reduce downtime and improve productivity in your facility.
- Identify: Use plant information to identify production bottlenecks.
- Review: Review inefficiencies and decide which one to act on.
- Act: Choose one action and address it with a possible solution.
- Track: Monitor, measure, and document progress with specific numbers.
- Adjust: Decide if the solution is working or needs to be redesigned.
Leveraging manufacturing intelligence can be used to improve an entire enterprise and supply chain. But without data, none of the above steps are possible.
Fortunately, implementing systems that gather, track and analyze data has never been easier or more affordable. With up-to-date information, you can begin to dig into data to see where existing processes are breaking down and what processes are operating optimally.
Smart manufacturing focuses on implementing tools that manage information across organizations and may include automation, machine learning and systems that provide real-time data. Examples include:
- Software as a Service (SaaS)
- Robotics
- Wearable technology
- Inventory control software
By harnessing data to make better operational decisions, businesses can improve supply chain management, improve production flow, predict equipment maintenance, track assets and become more competitive.
Interested in learning more? Visit our website.
1sourcevend’s point-of-use inventory solutions and 1sourcelive software are designed by distributors for distributors looking to differentiate themselves from the competition. Learn how we can help you apply inventory management software and American-made vending solutions to empower your customers. Request a Demo